In CNC machining customization, Design for Manufacturing (DFM) is a systematic approach that considers the needs of the manufacturing process from the product design stage and aims to optimize the manufacturing efficiency and cost-effectiveness of parts.
The core goal of DFM is to simplify the production process, reduce material usage, shorten production time and reduce costs through design without sacrificing product function and quality.
Key Principles of DFM
Simplify the design: The shape and structure of the parts should be simplified as much as possible during design, and unnecessary complex features should be reduced, which helps to reduce machining steps and time.
Standardize parts: Using standard parts and sizes can reduce the need for custom tools and molds, thereby reducing costs and speeding up production.
Reduce the number of parts: By integrating multiple parts into one, assembly costs and processing time can be reduced.
Optimize tolerances: Reasonable tolerance settings can reduce machining difficulty and improve machining efficiency.
Material selection: Choosing materials that are easy to machine and cost-effective can significantly reduce material and machining costs.
Design for assemblability: Ensure that the design is easy to assemble and reduce assembly time and costs.

Benefits of implementing DFM
Reduced costs: DFM helps reduce overall manufacturing costs by reducing material usage, simplifying machining processes, and reducing scrap.
Shortened time to market: Simplified design and production processes can shorten the time it takes for a product to go from design to market.
Improved quality and reliability: DFM encourages the design of more reliable products and reduces variations and defects in the production process.
Enhanced competitiveness: Cost-effectiveness and fast time to market can improve a company’s market competitiveness.
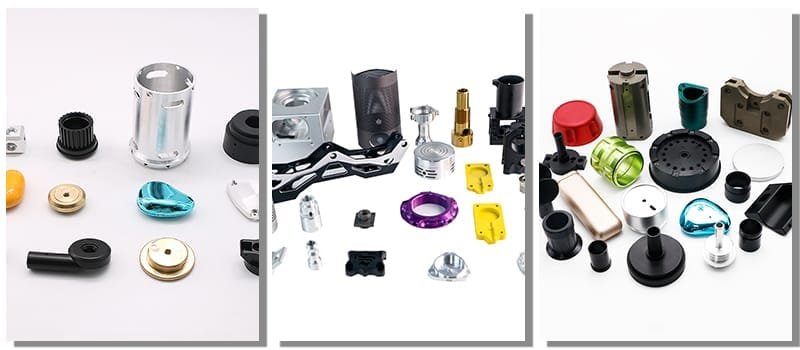
Application of DFM in CNC machining
In CNC machining, the application of DFM can be specific to the following aspects:
Programming optimization: Reduce machine movement and machining time by optimizing CNC programs.
Tool selection: Selecting the most appropriate tool can improve cutting efficiency and reduce the frequency of tool changes.
Processing path: Optimize machining paths to reduce machine idle time and increase material removal rate.
Batch production: Spread fixed costs such as machine setup and programming through batch production.
Adopting DFM strategies can achieve cost savings and efficiency improvements in CNC machining customization. By considering all aspects of manufacturing during the design phase, companies can optimize their product development processes, reduce waste, and deliver more competitive products and services.