Did you know that the use of transparent plastic materials in prototyping can enhance visibility and functionality, offering insights that opaque materials simply cannot? In today’s fast-paced manufacturing landscape, engineers and designers seek innovative solutions that not only meet performance standards but also enhance the communicative aspects of prototypes. As CNC (Computer Numerical Control) machining rapidly evolves, integrating transparent plastics into prototyping has become a game changer, dramatically influencing design validation, testing, and user experience.
CNC machining has transformed manufacturing processes, enabling high precision and repeatability when creating prototypes. While traditional materials have their advantages, transparent plastics — such as polycarbonate, acrylic, and poly(methyl methacrylate) (PMMA) — present compelling opportunities that many designers might not fully leverage. This blog will delve into why CNC prototypes can and should utilize transparent plastic materials, examining the benefits, challenges, and practical solutions to optimizing their use in various applications.
The Benefits of Transparent Plastics in CNC Prototyping
One of the most significant advantages of using transparent plastics in prototyping is visibility. Transparent materials allow stakeholders to observe internal features, mechanisms, and assemblies without needing disassembly. This is particularly beneficial in industries such as automotive, aerospace, and medical devices, where understanding the internal functioning of a prototype can lead to better designs and innovations.
Transparent plastics tend to be much lighter than their glass counterparts while still offering high durability and impact resistance. For applications requiring portability or weight reduction, such as drone components or wearables, transparent plastics are the ideal choice. Materials like polycarbonate can absorb shocks and withstand environmental challenges while maintaining clarity.
In industries where aesthetics are key—such as consumer electronics and luxury items—transparent plastics can provide a visually appealing finish. The ability to showcase the internal components of a product can enhance its appeal and communicate quality. This visual representation helps end-users appreciate the intricate designs that traditional materials may obscure.
CNC machining allows for the production of intricate shapes and designs. Transparent plastics can easily be manipulated using CNC equipment to create complex geometries. This customization capability enables engineers to test various design iterations efficiently, allowing for faster decision-making and pivoting along the design process.
While transparent materials can often be more expensive than conventional materials, the cost savings from reduced prototyping cycles and improved product development timelines may outweigh initial expenses. In the long run, understanding how a prototype behaves with transparent plastics can lead to savings in manufacturing costs and materials.
Practical Applications of Transparent Plastics in CNC Prototyping
In automotive prototyping, transparent covers for lighting components (such as headlights and taillights) enable designers to visualize and test light distribution and aesthetics during the prototype phase. Transparent plastics also allow easier inspections of internal components, like wiring and sensors, ensuring that all parts function correctly before moving into production.
The aerospace industry can benefit from using transparent plastics to prototype cockpit displays or external components. Creating clear panels over control systems allows engineers to assess clarity, visibility, and usability, identifying potential flaws or enhancements needed for optimal operational performance.
Medical devices often require sterile and clear materials for prototype testing. Transparent plastic allows engineers to visualize internal mechanisms like valves, tubes, and compartments crucial to a device’s performance. Furthermore, design verification is accelerated since prototypes can be inspected easily before production begins.
Consumer electronic devices increasingly incorporate transparent elements, like the casings of smartphones, tablets, and wearable devices. By using CNC prototypes made of transparent materials, designers can ensure that not only aesthetics but also the functionality aligns with user expectations, allowing the development of intuitive designs.
Challenges of Using Transparent Plastics in CNC Prototyping
While the benefits are compelling, there are several challenges to consider when working with transparent plastics in CNC machining:
Many transparent plastics require additional finishing processes to achieve optical clarity. Grinding and polishing may be necessary to remove surface imperfections from the CNC machining process. Proper machinery, skilled operators, and time investment are critical for achieving desired results.
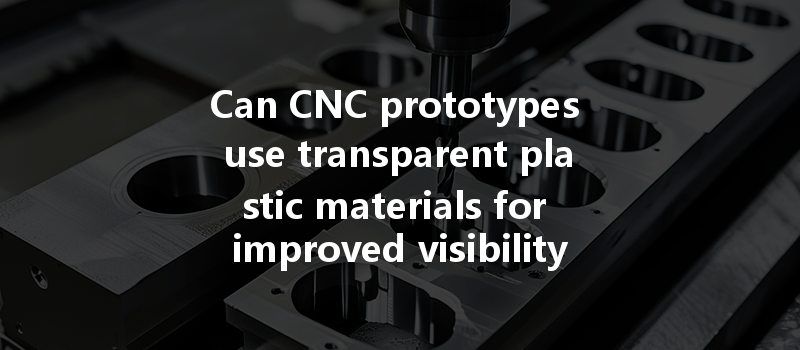
Certain transparent materials, especially polycarbonate, can be sensitive to heat during machining. High machining temperatures can lead to warping or deformation. Employing proper cooling methods or selecting suitable machining parameters will be necessary to mitigate these risks.
Different transparent plastics have distinct thermal, optical, and mechanical properties, which necessitates careful selection based on specific applications. It’s important to evaluate the specific requirements and characteristics for each project before choosing a material.
Transparent plastics are prone to scratches and surface damage, which can affect prototype performance and aesthetics. Employing protective measures during the machining and handling processes is essential to maintain product integrity.
Optimizing the Use of Transparent Plastics in CNC Prototyping
Understanding the attributes of various transparent plastics is crucial for successful CNC machining. Material selection should align with the specific requirements of the project. Common transparent plastics used for CNC prototyping include:
When machining transparent plastics, it’s essential to consider:
Post-processing can dramatically improve the quality of transparent prototypes. Techniques may include:
Before production, conducting thorough tests to assess the mechanical strength, optical clarity, and environmental resistance of prototypes is vital. User feedback should be gathered to identify any potential areas for improvement.
CNC machining combined with transparent plastics opens up new possibilities in prototyping across various industries. Enhancing visibility, design aesthetics, and the manipulation of complex geometries are just a few of the benefits that these materials offer. With a keen understanding of the challenges and strategic use of post-processing techniques, companies can fully leverage these materials to create functional and visually appealing prototypes that attract and engage consumers.
In a world that increasingly values transparency—not just in material but also in communication—using transparent plastics for CNC prototypes stands out as an innovative approach that merits consideration. As technology progresses and consumer demands change, it’s essential for designers and engineers to reflect on the ways materials can shape user experiences. By embracing the benefits of transparent materials today, we can build the foundations for tomorrow’s groundbreaking products.