CNC machining is revolutionizing the manufacturing industry with its precision, efficiency, and adaptability. As technology advances, the capabilities of CNC machines are expanding, allowing for the production of intricate designs and shapes that were previously unachievable. One area where this is particularly evident is in the machining of special-shaped aluminum alloy shells, which encompass complex curves and surfaces. This article will explore the intricacies of CNC machining in this domain, discussing its methodologies, advantages, challenges, and best practices, all while shedding light on YL Machining’s commitment to excellence in this field.
Understanding CNC Machining
What is CNC Machining?
Computer Numerical Control (CNC) machining is a subtractive manufacturing process where pre-programmed computer software dictates the movement of factory tools and machinery. This technology allows for high levels of precision and efficiency, making it ideal for various applications, including aerospace, automotive, and medical device manufacturing.
How Does CNC Machining Work?
CNC machines operate through a combination of computer codes and design software (such as CAD
The Role of Aluminum Alloys in CNC Machining
Aluminum alloys are used extensively in CNC machining due to their lightweight, strength, and excellent corrosion resistance. They can be easily shaped and manipulated, making them perfect candidates for producing intricate designs like shells and casings. Common aluminum alloys used in CNC machining include 6061, 7075, and 5052, each possessing unique properties suitable for various applications.
Processing Special-Shaped Aluminum Alloy Shells
Types of Special Shapes
Special-shaped parts often include components with unique curves, contours, and surface characteristics. Common applications for such features in aluminum alloy shells include housings for electronic devices, automotive parts, and aerospace components. The design complexity often requires CNC machining techniques that can handle both external and internal features with high precision.
Techniques for Machining Complex Shapes
Material Considerations
Machining special-shaped aluminum alloy shells requires a deep understanding of the material itself. For instance, 6061 aluminum offers good machinability and weldability, making it a favorite for many projects. In contrast, 7075 aluminum, while being stronger, poses challenges in machining due to its toughness, resulting in longer processing times and increased tool wear.
The Role of Tooling
The choice of tooling is paramount in successfully machining complex shapes. Solid carbide tools are often preferred for their durability and precision. Specialized end mills and inserts designed for specific profiles enable the production of characteristics like contours and fillets with high accuracy.
Advantages of CNC Machining for Special Shapes
CNC machining presents numerous advantages when producing special-shaped aluminum alloy shells:
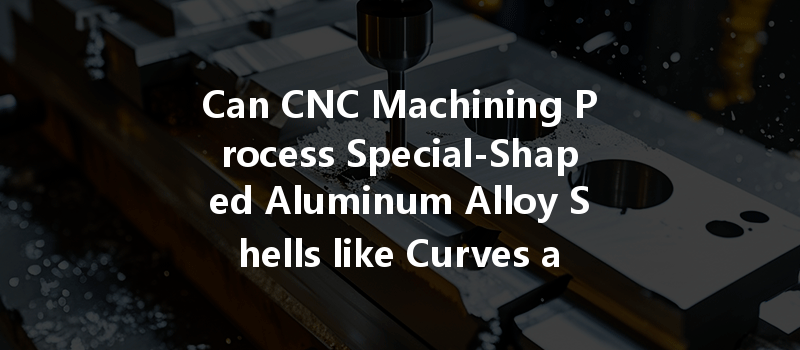
Challenges in CNC Machining of Special-Shaped Aluminum Alloys
While CNC machining offers significant advantages, it is not without its challenges:
Tool Wear and Maintenance
Aluminum alloys, particularly high-strength variants, can lead to increased tool wear. Manufacturers must carefully monitor tool conditions and apply effective maintenance strategies to prolong tool life and quality, significantly affecting production efficiency.
Surface Finish Requirements
Special-shaped components often require specific surface finishes, which may necessitate additional processes such as polishing or coating. Achieving the desired finish can be challenging and necessitates advanced knowledge of finishing techniques.
Design Complexity and Programming
Designing components with unique curves and shapes can complicate programming. A detailed understanding of both the machining capabilities and the design requirements is crucial for an optimal outcome.
Thermal Management
CNC machining generates heat, and excessive heat can affect the machining process and the properties of the aluminum alloy being processed. Proper cooling methods must be employed to mitigate thermal effects and maintain machining quality.
Best Practices for CNC Machining of Special-Shaped Aluminum Alloys
To successfully manufacture special-shaped aluminum alloy shells, the following best practices can be implemented:
CNC machining is invaluable for producing special-shaped aluminum alloy shells, thanks to its unmatched precision and ability to handle intricate designs. At YL Machining, we harness these capabilities to provide our clients with high-quality components tailored to meet their specific application needs. With a focus on continuous improvement and the latest technological advancements, we ensure that our manufacturing processes align with industry standards while striving for excellence.
The ever-evolving nature of CNC machining presents exciting opportunities, particularly as new materials and technologies emerge. This field is poised for growth, making it essential for manufacturers to adapt and innovate continuously. As the industry expands, the ability to process unique shapes and surfaces will only become more crucial in meeting the demands of modern manufacturing.
By understanding the complexities and best practices associated with CNC machining special-shaped aluminum alloy shells, businesses can leverage this technology to enhance product quality, operational efficiency, and ultimately, their competitive edge in the marketplace.