Did you know that the CNC (Computer Numerical Control) machining industry is projected to reach $117.2 billion by 2027? This dramatic increase underscores a significant trend: the rising demand for custom-engineered, high-precision parts across various sectors, including aerospace, automotive, and medical devices. As technology advances, manufacturers are faced with increasingly complex designs that require precision and reliability. This article explores whether CNC custom machining can effectively handle high-precision parts customization with complex shapes, analyzing the capability of CNC technology, the materials involved, and the best practices for achieving optimal results.
Understanding CNC Machining
CNC machining is a subtractive manufacturing process where a computer program controls the movement of machinery and tools. Unlike traditional machining processes that rely on manual operation, CNC machining automates the entire process, allowing for greater accuracy, consistency, and efficiency.
Key Components of CNC Machining
Advantages of CNC Machining in Producing Complex Shapes
High-Precision CNC Machining: Process Breakdown
Creating high-precision parts begins in the design phase. The designer must take into consideration not just the aesthetic aspects of the part but also its functionality and how it will be made.
Once the design is ready, the next step is tool path generation in the CAM software. Here, the programmer ensures:
Before the CNC machine begins processing, it’s crucial to properly set it up:
It’s during the actual machining that the custom shapes start to take form.
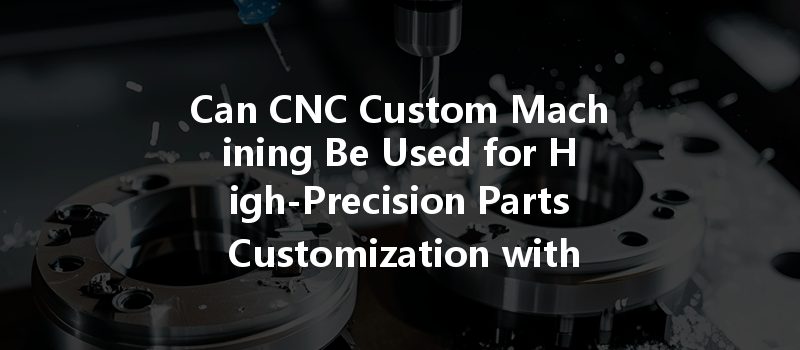
In CNC machining, ensuring the precision of the final product through rigorous quality checks is critical:
Challenges of CNC Machining for Complex Shapes
While CNC machining is robust and capable, there are challenges in customization of high-precision parts with complex shapes:
Complex shapes often require specialized tools, which can wear down more quickly than standard tools. Continuous monitoring and timely tool replacement are essential to maintain the quality of production.
Setting up CNC machines for custom parts—especially intricate designs—can be time-consuming. Ensuring that all configurations are correct and that workholding systems are secure requires a significant amount of planning.
Different materials behave in unique ways under machining processes. For example, softer materials like plastics are easier to machine but may not hold tolerances as well as harder metals, which can be more challenging to work with.
While CNC machining efficiency has come a long way, producing complex custom pieces may still involve higher costs. The initial setup, programming, and tooling can add to the expense, influencing the budget for projects.
Best Practices for High-Precision CNC Machining
To maximize efficiency and quality in high-precision parts customization, several best practices can be adhered to:
Ensuring the machinists and programmers are well-trained in the latest technologies and techniques will lead to better decision-making in the programming and machining processes.
Incorporate design for manufacturability principles early in the design phase to avoid complications down the line and ensure seamless customization of complex parts.
Implementing regular inspections at various stages of the machining process helps catch any issues that may arise, allowing for adjustments before defects escalate.
The latest CAD/CAM software tools can significantly enhance both design and machining workflows. Staying updated with technological advancements ensures that the production process remains competitive.
The ability for CNC custom machining to manufacture high-precision parts with complex shapes lies at the intersection of sophisticated technology, advanced materials, and refined technical skills. By embracing best practices, investing in training, and selecting the right tools and technologies, manufacturers can capitalize on the profound advantages offered by CNC machining.
In today’s highly competitive landscape, understanding the nuances of CNC machining not only serves as a tool for production but as a strategic advantage in delivering quality and innovation. As industries evolve, so too will the requirements for more complex, high-precision parts. This makes it imperative for engineers and manufacturers to consider CNC machining as a viable solution for their customization needs.
Remember, detailed planning and skilled operation are essential for making the most out of CNC custom machining technology. By continuously refining both your machining process and design principles, you can set your business on a path toward efficiency, quality, and success in a demanding market.
—