As someone who’s been in the machining industry for years, I can confidently say that CNC machining is both an art and a science. While it’s incredibly precise, achieving consistent, high-quality results—especially when working with aluminum—requires more than just hitting the start button on your CNC machine. From my experience, there are several strategies that can significantly reduce errors in the machining process, whether you’re dealing with CNC machining, turning, 5-axis machining, or milling.
Have you ever experienced problems with parts not fitting, surface finishes falling short, or delivery timelines slipping because of reworks? If so, this guide is for you. Let me walk you through practical, hands-on tips to minimize machining errors.
1. Understanding the Challenges of Aluminum in CNC Machining
Aluminum is a favorite material for many industries due to its lightweight, corrosion resistance, and excellent machinability. However, working with aluminum isn’t always straightforward. Let me share a quick story: Early in my career, I underestimated aluminum’s thermal expansion. The result? Parts that didn’t match the specified tolerances.
So, what makes aluminum tricky?
- Thermal Expansion: Aluminum expands significantly with heat, which can lead to dimensional inaccuracies.
- Chip Adhesion: Aluminum’s softness makes it prone to chip buildup on the cutting tool, especially in turning and milling operations.
- Surface Scratches: Its malleability makes it vulnerable to scratches, reducing the visual and functional quality of the part.
Recognizing these challenges is the first step toward mitigating errors.
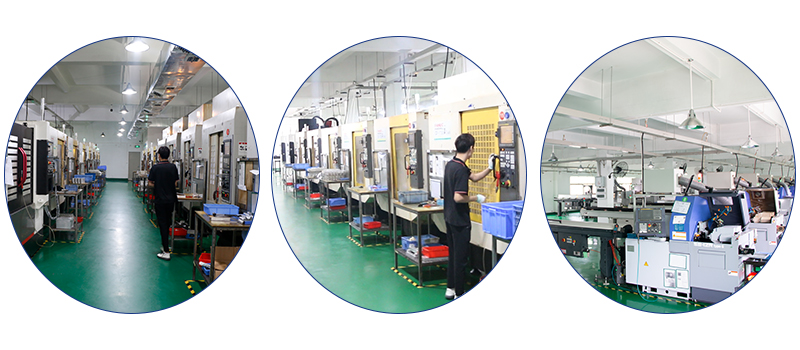
2. Choosing the Right Tools for the Job
When it comes to CNC machining, the tools you use can make or break your project. A dull or incorrect tool will lead to burrs, poor surface finishes, and increased chances of errors.
Here’s what to keep in mind:
- Tool Material: For aluminum, high-speed steel (HSS) and carbide tools are excellent choices. Carbide tools, in particular, are more resistant to wear and can handle higher speeds.
- Tool Coating: A good coating, like titanium nitride (TiN), can reduce chip buildup and improve heat resistance.
- Tool Geometry: Using tools with a high rake angle helps reduce cutting forces and minimizes material deformation.
Want a pro tip? Regularly inspect your tools for wear and replace them before they degrade. It’s far cheaper to replace a tool than to deal with reworks.
3. Optimizing Machining Parameters
Dialing in the right machining parameters is essential for precision. I’ve seen many machinists struggle with trial and error, but you don’t have to.
Speed and Feed Rates
- High spindle speeds work well for aluminum, but pairing them with the correct feed rate is crucial.
- Too slow, and you risk chip welding; too fast, and you might overheat the material.
Depth of Cut
- Keep your depth of cut within the tool’s capacity to avoid overloading and vibration.
Coolant Usage
- Aluminum generates heat quickly. Use a flood coolant to keep the material and tool cool while improving chip evacuation.
4. Invest in Precision Workholding
One of the most overlooked aspects of machining is workholding. If your part isn’t held securely, even the most precise machine won’t save you.
- Use Soft Jaws: These help prevent scratches and damage to the aluminum surface.
- Check for Runout: A misaligned workpiece can lead to tolerance issues. Always double-check your setup with a dial indicator.
- Vacuum Fixtures: For thin aluminum sheets, vacuum fixtures are a game-changer, preventing warping during machining.
5. Leverage Advanced Technologies: 5-Axis Machining
If you’re working on complex geometries, 5-axis machining can be a lifesaver. Unlike traditional milling, 5-axis machines allow for simultaneous movement along multiple axes, reducing the need for repositioning and ensuring higher accuracy.
When I first started using 5-axis machining, I was blown away by how much faster I could produce intricate parts with fewer errors. The key is to understand your machine’s capabilities and optimize your toolpaths accordingly.
6. Prioritize Quality Control at Every Step
Quality control isn’t just a final step—it should be baked into your process from the beginning.
Pre-Machining Checks
- Validate your CAD model and CAM program for errors.
- Perform a material inspection to ensure your aluminum stock meets the required standards.
In-Process Monitoring
- Use probing systems to measure critical features mid-operation.
- Employ sensors to detect tool wear or breakage before they cause damage.
Post-Machining Inspection
- Invest in a Coordinate Measuring Machine (CMM) to verify dimensions and tolerances.

7. How to Handle Surface Finishing Issues
Surface quality can make or break your product’s appeal and functionality. To avoid problems like rough finishes or visible machining marks:
- Use sharp tools and high speeds to achieve a smooth cut.
- Incorporate a finishing pass in your program.
- For enhanced aesthetics, consider bead blasting, anodizing, or other post-machining treatments.
8. Streamlining Communication with Your CNC Supplier
If you’re outsourcing your CNC machining work to a shop like YL-Machining, clear communication is essential. Share detailed drawings, specify tolerances, and discuss surface finish requirements upfront. It’s always better to over-communicate than risk misunderstandings.
9. Embrace a Continuous Improvement Mindset
No matter how experienced you are, there’s always room to improve. Collect feedback from your team and customers, and analyze past projects for areas where errors occurred.
Ask yourself:
- Could I have chosen better tools?
- Were my machining parameters optimal?
- Was my quality control process thorough enough?
10. Closing Thoughts
Minimizing errors in aluminum CNC machining isn’t just about having the best equipment—it’s about combining the right tools, techniques, and mindset. Whether you’re dealing with turning, milling, or 5-axis machining, every decision matters.
Next time you’re faced with a machining challenge, remember: precision is a journey, not a destination. And if you need help along the way, don’t hesitate to reach out to experts like us at YL-Machining. We’re here to turn your designs into reality—with accuracy you can count on.
What’s your biggest challenge in aluminum machining? Let’s discuss in the comments!