: The Unseen Challenges of Metal Wear Resistance
Did you know that equipment failure due to metal wear costs industries billions of dollars each year? Among the many factors that influence the longevity of metal components, wear resistance—essentially, how well a metal can withstand friction, pressure, or erosion—is pivotal. In industries ranging from aerospace to marine engineering, the choice of materials can significantly impact performance and operational costs.
One often-cited dilemma is the selection between 17-4PH stainless steel and 2205 duplex stainless steel. While both materials are renowned for their strength and corrosion resistance, their wear resistance characteristics can differ dramatically, depending on the application and service conditions. This blog will deep dive into the wear resistance of these two materials.
—
Understanding the Basics: 17-4PH and 2205 Duplex Stainless Steel
Before we compare the wear resistance of 17-4PH and 2205 duplex stainless steel, it is essential to understand what each material encompasses.
17-4PH Stainless Steel
17-4PH is a precipitation-hardening stainless steel that contains approximately 17% chromium and 4% nickel. This steel is known for its high strength, as well as excellent corrosion resistance, making it suitable for applications in sectors such as aerospace, chemical processing, and nuclear.
2205 Duplex Stainless Steel
On the other hand, 2205 duplex stainless steel is austenitic-ferritic stainless steel, containing about 22% chromium, 5% nickel, and 3% molybdenum. Its unique microstructure combines the properties of both austenitic and ferritic steels, giving it superior strength and corrosion resistance, particularly in aggressive environments.
—
Comparing Wear Resistance
Wear resistance is a broad category encompassing several forms of wear, including abrasion, erosion, and adhesive wear. When comparing 17-4PH and 2205, the context of their use—temperature, load, and corrosive environment—plays a pivotal role in determining which material is more advantageous.
Abrasive wear occurs when two materials are in contact, and one material wears away due to friction or debris between them. In applications involving frequent contacts—like gears, bearings, and valves—this can drastically affect performance.
Erosive wear results from particles striking a surface at high speed, causing material erosion.
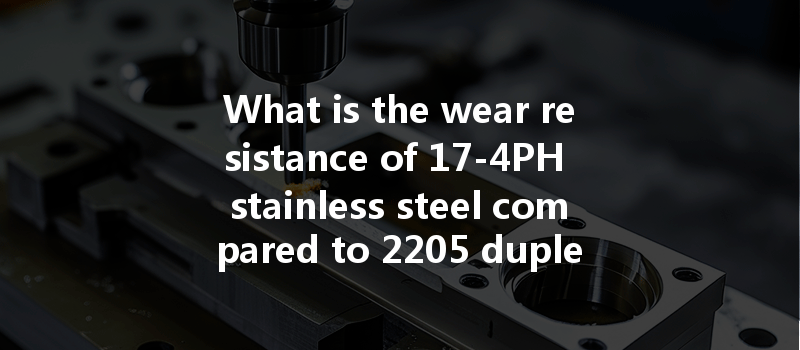
Adhesive wear occurs when two materials bond at the surface under pressure and then separate, pulling material from one or both components.
—
Application Profiles: Which To Choose?
The essence of selecting between 17-4PH and 2205 lies in the specific environmental and operational conditions.
—
: The Need for Material Insight
Ultimately, while both 17-4PH and 2205 duplex stainless steel boast remarkable features, the choice between them is contingent upon specific application requirements and environmental factors.
As we have explored, understanding the nuances of wear mechanics and the material properties can make a significant difference in selecting the right steel for your project.
Choosing the appropriate material can save companies from costly repairs and replacements caused by premature wear and ensure optimal performance and longevity. The implications of this decision extend beyond the workshop floor and into the profitability and sustainability of an operation. Thus, the importance of knowing the wear resistance characteristics of these steels cannot be overstated.
Think carefully about the conditions and functional requirements of your application, as every decision counts toward ensuring neither quality nor efficiency is ever compromised.