When it comes to engineering materials, the choice often boils down to two possible contenders: metals or plastics. One fascinating fact to consider is that copper stands out as one of the best conductors of electricity, with a conductivity rating of about 59.6 x 10^6 S/m. With that said, do you ever wonder how copper parts modify the processes in CNC machining when compared to plastic components?
In today’s blog, we’re going to dive deep into the comparison of CNC machining for copper parts against that of plastic machining, or the specific attributes of conductivity between the two. Together, we’ll understand how these differences impact various industries, reveal advantages and limitations of both materials, and plot a path for efficient machining solutions tailored to each material.
Understanding Conductivity: A Primer
Conductivity can be defined as a material’s ability to conduct electric current. It is a crucial property that dictates where and how materials can be applied in real-world applications. The conductivity of copper makes it a preferred choice in electrical applications, while plastics, generally considered insulators, find their utility where electrical conductivity is not a concern.
The conductivity properties of a material result mainly from its atomic structure and electron configuration. Metals like copper, with their free-moving electrons, allow electric current to flow with minimal resistance. Conversely, plastics tend to have tightly bonded electrons, making them non-conductive.
Conductivity in CNC Machining
“CNC” stands for Computer Numerical Control, a method that operates machine tools via computers executing pre-programmed sequences of machine control commands. When applied to copper and plastic, the differences in conductivity can lead to distinct machining behaviors, process decisions, and application suitability.
Copper is highly sought after for various industrial applications, especially those requiring excellent electrical conductivity, thermal conductivity, and corrosion resistance.
Benefits of CNC Machining Copper
Challenges in CNC Machining Copper
Plastic machining presents a myriad of solutions across multiple industries ranging from automotive to consumer electronics.
Benefits of CNC Machining Plastic
Challenges in CNC Machining Plastic
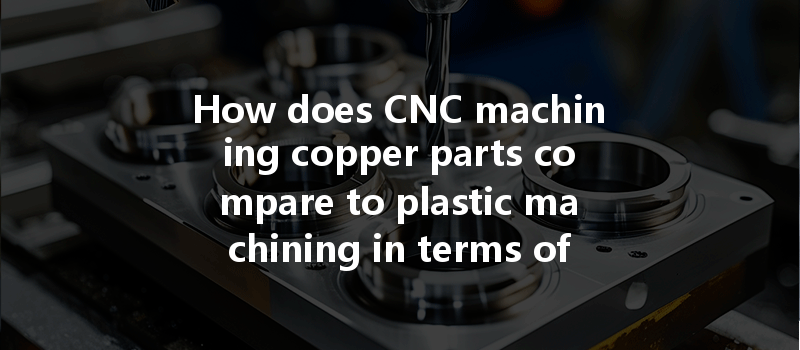
Comparing Conductivity: Copper vs. Plastic
When we get to the crux of the matter—conductivity—there’s a dramatic contrast between copper and plastic.
Applications Influenced by Conductivity
The choice between copper and plastic directly influences several industries; let’s examine some specific cases.
Electrical Engineering
In electrical engineering, copper reigns supreme. Applications such as wiring harnesses, circuit boards, and conductive paths rely on copper’s unparalleled conductivity to facilitate current flow, ensuring efficiency and reliability. On the other hand, plastics serve as insulation around wires, contributing to safety.
Automotive Industry
In automotive manufacturing, copper is used for electrical components, like alternators and batteries, requiring high conductivity. But in non-conductive applications like dashboards or seats, plastics are more prevalent.
Consumer Electronics
Similar to automotive, consumer electronics balance between copper’s conductive roles in circuit boards and plastic casings providing lightweight, durable enclosure.
Recommendations for Machining
Given the distinct properties and challenges that come with machining both copper and plastic, a tailored approach can optimize manufacturing and performance.
For Copper:
For Plastic:
CNC machining offers versatile solutions for fabricating both copper and plastic components. While copper’s outstanding conductivity dramatically enhances electrical applications, the lightweight and cost-effective properties of plastics deliver significant value in numerous industries. Each material performs uniquely under CNC machining conditions, influencing tool selection, machining processes, and overall product quality.
Ultimately, the decision between utilizing copper or plastic should hinge on the specific requirements of the application, desired properties, and budget considerations. As we strive for a precise and efficient machining process, understanding these differences lays the groundwork for informed choices.
As technology continues to evolve, the future holds the promise of new materials, enhanced machinery, and optimized processes. Engaging with these advancements will not only improve efficiency but also foster innovation in various fields that rely on precision machining.
In a rapidly changing manufacturing landscape, it’s important to think critically about material selection—understanding the conductivity of copper versus plastic may just be the step that leads to groundbreaking applications and technologies. Your production facilities, design teams, and end products will undoubtedly reap significant benefits from this knowledge.