Did you know that the global aerospace manufacturing market is projected to reach a staggering $1 trillion by 2030? As the demand for lightweight yet durable materials continues to rise, the aerospace industry must adapt to enhance production efficiency, reduce costs, and ensure safety—enter CNC machining. But what exactly are the benefits of CNC machining for customized aerospace metal components? In this comprehensive guide, we’ll delve into the details, explore how this technology is transforming the aerospace sector, and understand why it is a critical consideration for manufacturers looking to thrive in a competitive market.
The Evolution of Aerospace Manufacturing
The aerospace industry has witnessed remarkable transformations over the decades. From the early days of handcrafted aircraft parts to the modern era of mass production and automation, the quest for efficiency and precision has been relentless. As aircraft designs become increasingly complex and the demand for customization grows, manufacturers are turning to innovative technologies like CNC (Computer Numerical Control) machining to meet these challenges effectively.
CNC machining leverages computer software to control machining tools with precision, ensuring that components are manufactured to exact specifications. This not only streamlines the production process but also enhances the overall quality of aerospace components.
Understanding CNC Machining
Before diving deep into the benefits, let’s clarify what CNC machining entails. CNC machining encompasses a variety of processes, including milling, turning, drilling, and grinding. It operates with the following key components:
Key Processes in CNC Machining
Benefits of CNC Machining in Aerospace Component Production
One of the most significant advantages of CNC machining is the extraordinary precision it offers. Aerospace components require exact specifications, and even the slightest imperfections can lead to catastrophic failures. CNC machines can replicate designs consistently, ensuring that each part meets stringent quality standards. This level of accuracy is crucial in the aerospace sector, where safety is paramount.
With the capability to produce bespoke components, CNC machining shines in customization. Aerospace manufacturers often require parts that are tailored to specific designs and functions. CNC machining can easily accommodate these requirements, whether it’s creating unique housing for avionics or specialized engine components. The ability to switch designs with software programming makes CNC machines incredibly flexible.
In a competitive market, time is often as valuable as money. CNC machining significantly reduces production time by automating processes that were previously manual. Once a design is programmed, machines can operate continuously, producing high volumes of components rapidly. This increased speed leads to shorter lead times and faster time-to-market, giving manufacturers an edge over competitors.
While the initial investment in CNC machines can be substantial, the long-term cost benefits are undeniable. The automation of processes minimizes labor costs and reduces the chances of human error affecting the quality of the components. Additionally, CNC machining maximizes material utilization, reducing waste—a vital consideration in today’s environmentally conscious marketplace.
The aerospace industry requires a range of materials, including high-strength alloys, lightweight composites, and various metals. CNC machines can be equipped with different cutting tools suitable for various materials, allowing manufacturers to work with titanium, aluminum, steel, and others without significant adjustments to the machinery. This adaptability makes CNC machining a robust solution for diverse aerospace applications.
Safety is a critical concern in aerospace manufacturing. Components must comply with strict regulations to ensure the safety of passengers and crew. CNC machining integrates advanced monitoring systems that ensure compliance with safety standards throughout the manufacturing process. This monitoring enables manufacturers to trace and document each phase of production, from raw materials to the final product.
Once a CNC program is generated, replicating the same part takes minimal adjustments. This reproducibility is essential for producing replacement parts for aircraft, ensuring that the newer components match perfectly with the older ones. Whether it’s for maintenance or repairs, this reliability is crucial for the sustainability of aircraft operations.
As market demand fluctuates, manufacturers must adapt their production volumes. CNC machining allows for quick adjustments to be made by altering programs and setups without the need for significant downtime or reconfiguration. This makes scaling production capabilities in response to market needs incredibly straightforward.
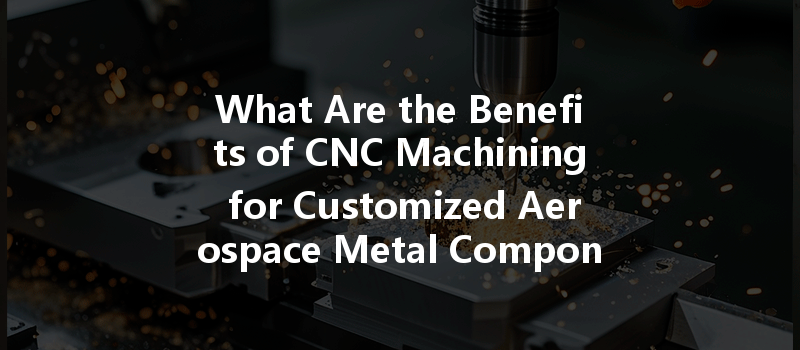
CNC machining often works harmoniously with other advanced manufacturing technologies, such as additive manufacturing (3D printing) and robotics. This integration facilitates innovative designs that may not have been possible with traditional methods, leading to new possibilities in aerospace component development.
Real-World Applications of CNC Machining in Aerospace
The benefits of CNC machining are not merely theoretical; they have been applied effectively in various aerospace projects. Here are some illustrative case studies:
Case Study 1: Aircraft Engine Components
Leading aerospace manufacturers have employed CNC machining for fabricating complex engine components with intricate designs. Critical parts that require precision, such as turbine blades, are produced using multi-axis CNC machines. These machines allow for the manufacturing of aerodynamic shapes, improving fuel efficiency and engine performance.
Case Study 2: Avionics Housings
CNC machining has played a vital role in producing housings for avionics equipment. The precision needed to accommodate electronic components and ensure compatibility with other systems is achieved through CNC milling and turning processes. This ensures that crucial functionalities are maintained in harsh operating environments.
Case Study 3: Fuselage and Wing Structures
For fuselage and wing components, manufacturers rely on CNC machining to create lightweight, high-strength structures that meet specific regulations. The versatility of CNC technology allows for various structural components to be machined from different materials, contributing to aircraft efficiency.
Challenges Faced in CNC Machining for Aerospace
Despite its numerous benefits, CNC machining does face challenges in aerospace manufacturing:
The setup costs for CNC machining can be high, particularly for advanced multi-axis machines. Manufacturers may need to allocate significant budgets to acquire equipment, software, and maintenance. This upfront investment can be a barrier for smaller companies.
Operating CNC machines and programming them requires skilled personnel. There is a demand for trained professionals who can handle the complex programming and maintain equipment efficiently. Companies may face challenges in staffing qualified personnel.
While CNC machining can work with various materials, some high-performance alloys may be difficult to machine due to their properties, leading to longer processing times and potentially higher costs. Finding a solution for these challenging materials is crucial for aerospace manufacturers.
The Future of CNC Machining in Aerospace
As technology continues to evolve, the future of CNC machining in the aerospace industry looks promising. Some anticipated trends include:
Automation will continue to play a vital role, particularly with the integration of AI and machine learning. This will further enhance efficiencies, reduce human error, and improve the overall capabilities of CNC machines.
With increasing pressure to reduce waste and lower carbon footprints, CNC machining will likely align with sustainable practices. This may involve advancements in recycling materials and optimizing processes to reduce environmental impact.
The aerospace industry will continue to explore advanced materials and manufacturing techniques, such as hybrid manufacturing, where CNC machining is combined with additive manufacturing. This will open pathways for new innovative designs.
CNC machining has revolutionized the aerospace industry, providing manufacturers with the tools to create high-precision, customized metal components efficiently. From ensuring safety compliance to enhancing production speed and flexibility, CNC machining is an indispensable technology for modern aerospace manufacturing.
As we look to the future, it is vital for manufacturers to consider adopting CNC machining practices to remain competitive in an ever-evolving market. With its numerous advantages and the potential for continued innovation, CNC machining represents not just a solution, but a pathway to the future of aerospace manufacturing.
In summary, understanding the nuances of CNC machining and its applications can empower manufacturers to make informed decisions regarding production techniques and materials. As the aerospace sector grows, so does the importance of CNC manufacturing—a pivotal consideration for companies striving to excel in this high-stakes industry.