Did you know that the aerospace industry is one of the most technologically advanced fields in the world, continuously pushing the limits of design and manufacturing? According to the Aerospace Industries Association, the U.S. aerospace and defense industry contributed over $900 billion to the economy in 2021 and is expected to grow exponentially in the coming years. These advancements are largely driven by innovations in manufacturing processes, such as CNC (Computer Numerical Control) machining, which offers unparalleled precision, efficiency, and flexibility in producing customized metal components.
In this exhaustive blog post, we will explore the multitude of benefits that CNC machining provides for customized aerospace metal components. We will discuss how this technology enhances precision, reduces waste, and ultimately leads to superior product quality, while addressing common challenges faced in aerospace manufacturing. From understanding the basic principles of CNC machining to advanced applications and future trends, this blog will serve as a comprehensive guide for aerospace engineers, manufacturers, and enthusiasts.
Part 1: Understanding CNC Machining
1.1 What is CNC Machining?
CNC machining is an advanced manufacturing process that utilizes computer-controlled tools to create parts and components. It allows for the automated and precise shaping of materials such as metal, plastic, and wood, by following detailed CAD (Computer-Aided Design) models or blueprints. The use of CNC machines—such as mills, lathes, and routers—eliminates the need for manual operations, significantly increasing the quality and speed of production.
1.2 The Principles of CNC Machining
At its core, CNC machining operates on several fundamental principles:
1.3 Types of CNC Machining
In the context of aerospace metal components, various CNC machining processes can be employed, each with unique advantages:
Part 2: Benefits of CNC Machining for Aerospace Components
2.1 Enhanced Precision and Accuracy
One of the primary benefits of CNC machining in aerospace applications is the precision it offers. Aerospace components are subject to strict tolerances, as even the slightest deviation can lead to disastrous consequences. CNC machines can achieve tolerances of ±0.001 inches or less, ensuring that every part meets specific design requirements. This level of accuracy is crucial for components like turbine blades, structural parts, and assemblies, where precision is paramount to operational safety and efficiency.
2.2 Lower Production Costs
While the initial investment in CNC machinery can be substantial, the long-term savings often outweigh the costs. CNC machining can produce parts at a lower cost by:
2.3 Flexibility and Customization
Aerospace manufacturers frequently deal with a variety of specialized components tailored for specific applications. CNC machining offers significant flexibility, allowing for:
2.4 Improved Quality Control
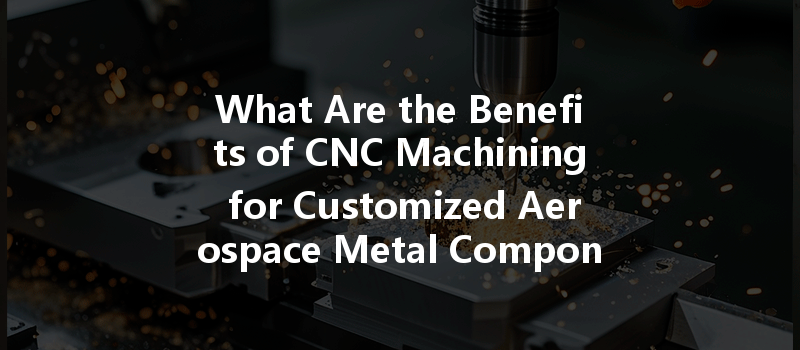
CNC machining comes equipped with many software-driven capabilities that offer enhanced quality control processes, including:
2.5 Reduced Lead Times
The aerospace industry cannot afford to delay projects, especially given the high stakes involved. CNC machining helps minimize lead times through:
Part 3: Common Challenges in Aerospace CNC Machining and Solutions
3.1 Material Limitations
Challenge: Aerospace applications often involve high-strength and lightweight materials such as titanium, aluminum, and composite materials, which can be challenging to machine.
Solution: Employ advanced machining strategies and cutting tools designed specifically for these materials. Coated carbide tools, for instance, can enhance cutting performance and extend tool life, while effective cooling systems can mitigate heat generation.
3.2 Tool Wear and Maintenance
Challenge: High-volume production can lead to accelerated tool wear and increased replacement costs.
Solution: Implement a preventative maintenance program to regularly inspect and service CNC machinery and tools, ensuring optimal performance. Utilization of smart monitoring technologies can also facilitate the timely replacement of worn tools, minimizing downtime.
3.3 Complex Designs
Challenge: As designs grow increasingly complex, ensuring that CNC machines can handle intricate geometries can be challenging.
Solution: Invest in high-end CNC machines equipped with 5-axis capabilities, which can maneuver around complex shapes and reduce the need for multiple setups.
Part 4: The Future of CNC Machining in Aerospace
4.1 Integration with Industry 4.0
The advent of Industry 4.0—the ongoing fourth industrial revolution—brings forth advancements in the integration of CNC machines with the Internet of Things (IoT), artificial intelligence (AI), and data analytics. These technologies promise to revolutionize the aerospace sector by:
4.2 Eco-friendly Practices
As sustainability takes center stage, the aerospace industry is also shifting toward more eco-friendly practices. CNC machining plays a vital role in this evolution by:
In conclusion, CNC machining offers myriad benefits for the aerospace industry, from enhanced precision and cost reduction to improved flexibility and quality assurance. As the industry continues to evolve and tackle new challenges, the role of CNC technology will only become more critical. Understanding the capabilities and limitations of CNC machining can empower manufacturers to make informed decisions, push boundaries, and effectively respond to the needs of an ever-changing market landscape.
The insights provided in this blog are just the tip of the iceberg when considering the far-reaching implications of CNC machining in aerospace manufacturing. Whether you’re an industry veteran or a newcomer to the field, acknowledging and implementing these advanced machining solutions can propel your projects forward, ensuring safety, efficiency, and success in the exciting world of aerospace.
Remember, the future is not just about building sophisticated machinery; it’s about building safer aircraft that pave the way for a more connected, efficient world. Embracing CNC machining technology is vital in this journey, and it’s time to consider how its transformative powers can benefit your aerospace projects.