Intro: A Question to Ponder
Did you know that manufacturing facilities around the globe are losing approximately 20–30% of their productivity due to inefficiencies in their CNC machining processes? This staggering statistic highlights a critical aspect of modern-day manufacturing, especially when working with specialized materials like 2205 duplex stainless steel.
In today’s high-paced, cost-efficient production environment, improving the production efficiency of CNC machining processes is essential not only for maximizing output but also for ensuring consistent quality. But how exactly can you enhance the efficiency of CNC machining when working with a complex alloy like 2205 duplex stainless steel?
Understanding 2205 Duplex Stainless Steel
What is 2205 Duplex Stainless Steel?
Before diving into techniques for improving machining efficiency, it’s crucial to understand the material in question—2205 duplex stainless steel. This alloy, composed of approximately 22% chromium, 5% nickel, and a small percentage of molybdenum, is renowned for its high strength, excellent corrosion resistance, and ability to withstand stress. These properties make it an excellent choice for various applications, particularly in the oil and gas industries.
Why Use 2205 Duplex Stainless Steel?
The high durability and excellent performance attributes of this alloy contribute to its rising popularity. However, these very characteristics can present substantial challenges in CNC machining, including tool wear and the risk of poor surface finishes.
With the right techniques and strategies, it is possible to enhance production efficiency while achieving the desired quality standards in parts manufactured from 2205 duplex stainless steel.
Factors Affecting CNC Machining Efficiency
Tool material and geometry play a significant role in the efficiency of CNC machining operations. Using high-quality carbide tools designed to withstand thermal stress and maintain sharpness is vital.
Key parameters, including cutting speed, feed rate, and depth of cut, need careful consideration. The optimal settings for 2205 duplex stainless steel often differ from those recommended for other materials, necessitating specific adjustments for effective machining.
Correct coolant application can drastically improve tool life and finish quality, especially when machining materials like 2205 duplex stainless steel that tend to generate heat.
Using well-maintained and correctly calibrated machines reduces erroneous production and enhances output efficiency. Regular inspection and preventive maintenance are essential for achieving this.
Well-trained CNC machinists are critical to improving production efficiency. Their hands-on experience in machining complex alloys such as duplex stainless steel can make a world of difference.
Strategies for Improving Production Efficiency
To capitalize on the advantages of 2205 duplex stainless steel, the following strategies can be implemented:
Choosing the right tooling is perhaps one of the most crucial steps in enhancing machining efficiency. When working with 2205 duplex stainless steel, consider the following:
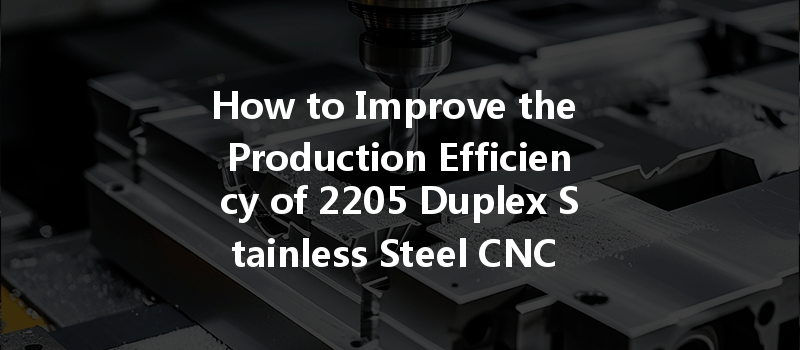
Study the specific machining parameters that work best for 2205 duplex stainless steel. This involves:
Implementing superior cooling strategies can help keep temperatures down during machining. Techniques include:
Regularly scheduled maintenance checks are essential to ensure your CNC machines run smoothly. During these checks, emphasize the following:
An often-overlooked factor in improving production efficiency is the training of CNC operators. Investing in training programs can yield dividends in machining performance by ensuring operators:
In manufacturing, continuous improvement is key. Implementing methodologies like Lean Manufacturing and Six Sigma can help identify waste and optimize processes step by step. Techniques include:
: The Path Forward
In conclusion, improving the production efficiency of CNC machining for 2205 duplex stainless steel revolves around a blend of advanced techniques and best practices. By focusing on optimized tool selection, fine-tuning machining parameters, employing effective cooling strategies, conducting regular maintenance, investing in operator training, and embracing continuous improvement practices, manufacturers can significantly boost their output while maintaining the high-quality standards required for this complex alloy.
As the industry continues to evolve, embracing these strategies can provide a competitive edge, ultimately leading to enhanced productivity and profitability. Considering that 20–30% of productivity can be lost due to inefficiencies, addressing these areas is not only rewarding—it’s critical for the future of machining operations focused on specialized materials like 2205 duplex stainless steel.
By fostering a culture of excellence and continuous learning, your operation can thrive in an ever-demanding market. Remember, it’s the small, intentional improvements that lead to significant long-term gains!