: An Interesting Statistic
Did you know that about 30% of machined components fail to meet dimensional tolerances due to material deformation during machining? In the world of CNC machining, especially when it comes to softer metals like 3003 aluminum, controlling deformation is crucial to ensuring precision and quality. For manufacturers and engineers, understanding how to mitigate this challenge is paramount. As we delve into the complexities of CNC machining aluminum, particularly 3003 alloy, we will explore effective techniques and insights that can significantly reduce deformation, enhance precision, and foster a smoother production process.
Understanding 3003 Aluminum
Before we dive into the solutions for controlling deformation, let’s first understand what 3003 aluminum is and why it is widely used in CNC machining.
3003 aluminum is an alloy that comprises around 1.2% manganese, making it one of the most versatile and used aluminum alloys. It is known for its excellent corrosion resistance, good workability, and moderate strength. Most importantly, it is favored in applications requiring moderate strength with a high degree of formability.
However, the softness of 3003 aluminum can lead to significant deformation during CNC machining if not properly managed. Understanding the characteristics of 3003 aluminum is the first step in preventing deformation during the machining process.
Causes of Deformation in CNC Machining
To effectively control deformation, it is crucial to understand the underlying factors that contribute to it. Here are the major causes:
Strategies to Control Deformation
Now that we have identified the potential causes of deformation, let’s discuss strategies to control them effectively during CNC machining of 3003 aluminum.
Selecting the right tools for machining 3003 aluminum is vital. The following factors should be considered when optimizing tool selection:
The cutting speed and feed rate significantly influence the machining results and deformation. Here are some recommended practices:
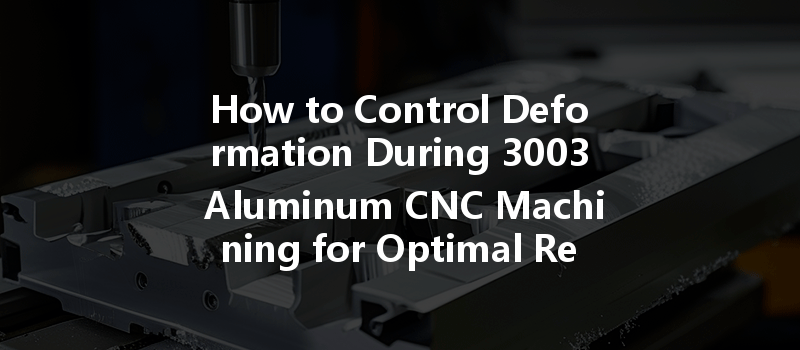
Heat management during machining is critical. Here are several approaches to control thermal expansion:
Improper clamping can lead to unwanted deformation. To optimize clamping techniques:
Machining sequences can influence the degree of deformation experienced:
Before diving into full production, leveraging digital tools and simulation can provide insights into potential deformation issues:
Measuring Success and Adjusting Techniques
Although the strategies mentioned above can significantly reduce deformation in CNC machining of 3003 aluminum, testing, and recalibrating processes are imperative.
: The Importance of Controlling Deformation
In summary, controlling deformation during CNC machining of 3003 aluminum is not just a technical requirement; it is a vital aspect of maintaining quality, efficiency, and consistency in manufacturing processes. By employing a combination of optimized tool selection, precise control of machining parameters, proper thermal management, and effective clamping solutions, manufacturers can reduce deformation and enhance the overall machining process.
Reflecting on the statistics we began with, addressing deformation issues can lead to substantial cost savings, increased production efficiency, and better product quality. For engineers and manufacturers, mastering these techniques is essential not only for immediate production goals but also for achieving long-term success in the competitive landscape of CNC machining.
Our exploration of deformation control is not just a technical lesson; it is an essential investment in the future of precision engineering. So, contemplate the methods discussed and apply them thoughtfully – your projects and your bottom line will thank you.