—
Interesting Opening
Did you know that the global demand for duplex stainless steel has been steadily rising, outpacing conventional austenitic stainless steels like 304 by over 25% in certain industrial sectors? As industries adapt to the growing need for stronger, more corrosion-resistant materials, understanding the practical differences in machining various grades of stainless steel becomes crucial for manufacturers. This article investigates the machining difficulties of 2205 duplex stainless steel compared to 304 stainless steel, uncovering essential insights for engineers and machinists alike.
—
Machining is integral to modern manufacturing, influencing product quality, efficiency, and cost-effectiveness. Among the multitude of materials processed, stainless steels stand out for their versatility and widespread application. However, they do not come without challenges. In this article, we will explore the specific machining difficulties associated with two popular stainless steel types: 2205 duplex stainless steel and 304 stainless steel.
As we delve deeper, we will align the distinctions in their composition, mechanical properties, and how these factors contribute to their machinability. This exposition aims to equip engineers, machinists, and decision-makers with vital knowledge to optimize manufacturing processes while avoiding costly errors.
—
1.1 Composition and Types
Stainless steel is an iron alloy that contains a minimum of 10.5% chromium, which confers its remarkable corrosion resistance. Various types of stainless steel are classified based on their microstructures, mainly austenitic, ferritic, and duplex. The austenitic group includes grades like 304, while duplex grades consist of both austenitic and ferritic structures, like
1.2 Applications of Stainless Steel
Stainless steels are commonly used in environments requiring excellent corrosion resistance, such as marine applications, chemical processing, and food industries. Thus, understanding which grade suits specific conditions is essential for optimal performance.
2.1 Chemical Composition
2205 duplex stainless steel consists of approximately 22% chromium, 5% nickel, and 3% molybdenum. This unique combination results in a microstructure that offers high strength and improved resistance to corrosion and stress corrosion cracking.
2.2 Mechanical Properties
With a yield strength typically twice that of 304 stainless steel, 2205 exhibits remarkable durability. Its tensile strength ranges from 80 to 120 ksi, making it suitable for high-stress applications.
2.3 Applications and Advantages
Due to its high strength and resistance, 2205 is extensively used in pulp and paper, oil and gas, and marine industries. The significant resistance to pitting and crevice corrosion allows it to perform well even in challenging conditions.
3.1 Chemical Composition
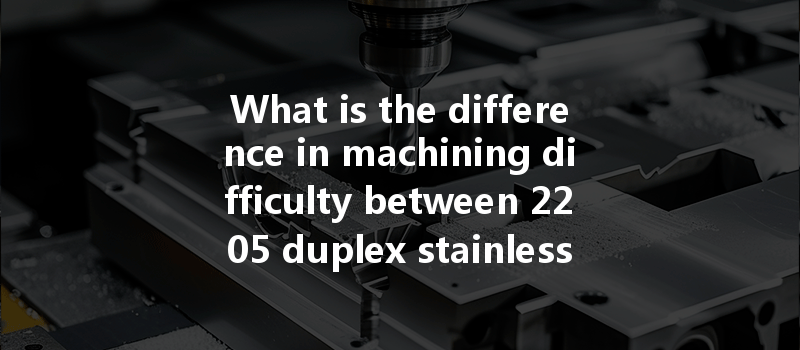
304 stainless steel is predominantly composed of 18% chromium and 8% nickel, contributing to its excellent corrosion resistance and weldability. It is one of the most widely used austenitic stainless steels.
3.2 Mechanical Properties
Although 304 exhibits good strength, its yield strength is about half that of 2205, ranging from 30 to 50 ksi. It is not as robust under stress but remains a preferred choice for less demanding applications.
3.3 Applications and Advantages
Commonly used in kitchen equipment, food processing, and architecture, 304 stainless steel’s formability and resistance to oxidation make it universally suitable.
4.1 Tool Wear and Material Removal Rates
When machining, duplex stainless steels like 2205 can be more abrasive, leading to pronounced tool wear. The hardness of 2205 can demand higher cutting forces compared to softer 304, resulting in slower material removal rates and lower tool life.
4.2 Chip Formation and Control
Machining 304 often yields more manageable chips, thereby facilitating easier control during the machining process. In contrast, 2205’s chips may be tougher to handle due to their hardness, requiring advanced chip control techniques.
4.3 Surface Finish and Tolerance Issues
Achieving a smooth surface finish on 2205 can be more challenging than on
5.1 Best Practices for Machining 2205
To effectively machine 2205 duplex stainless steel, consider the following guidelines:
5.2 Best Practices for Machining 304
With 304 stainless steel, operators should:
6.1 Choosing the Right Cutting Tools
The selection of cutting tools is critical for both 2205 and 304 stainless steels. High-speed steel tools may work for 304, but for duplex grades, high-performance carbide or cermet tools are often preferable.
6.2 Use of Coolants and Lubricants
Using a suitable coolant can greatly influence the machining outcomes for both materials. For difficult-to-machine materials like 2205, high-pressure coolant systems can improve outcomes significantly.
Real-life examples can illustrate the differences in machining challenges:
In summary, while both 2205 duplex stainless steel and 304 stainless steel are widely used in various industries, their machining characteristics differ significantly. Engineers and machinists must be aware of these differences to choose suitable materials based on application requirements while ensuring efficient manufacturing processes.
Final Thoughts
Understanding the intricate differences in machining difficulty between these materials can lead to better decision-making in production processes. Whether selecting tools, determining settings for CNC machinery, or managing production efficiency, this knowledge is essential for optimizing operations in an increasingly competitive landscape.
As manufacturers continue to incorporate advanced materials into their workflows, diving deeper into the specifics of CNC machining not only reduces waste but also enhances product quality and customer satisfaction. This blog serves as a vital resource, helping industry professionals navigate the complexities of machining duplex versus austenitic stainless steels.
—
FAQs
By keeping these critical aspects in mind, you can ensure production processes are optimized, ultimately fostering a path towards innovation in manufacturing practices.