Introductory Hook: The Growing Demand for Precision in Soft Material CNC Machining
Did you know that the global CNC machining market is expected to reach a staggering $100 billion by 2026? This rapid growth is heavily influenced by the increasing demand for precision engineering across various industries, including aerospace, automotive, and medical devices. Among the many materials being machined, soft materials like aluminum, plastics, and certain composite materials play a pivotal role. However, machining these soft materials presents a unique set of challenges. In this blog, we will explore the special requirements and precautions necessary for successfully processing soft materials in CNC machining to enhance precision, improve efficiency, and minimize waste.
Understanding Soft Materials in CNC Machining
What Are Soft Materials?
Soft materials, in the context of CNC machining, refer to materials that have lower hardness levels compared to traditional metals like steel or iron. Common examples include:
Understanding the characteristics of these materials is crucial before any machining process begins.
The Unique Challenges Faced During Machining
Processing soft materials comes with its own set of challenges:
Special Requirements for Processing Soft Materials
Tool Material
Choosing the right cutting tool is critical in CNC machining of soft materials. Common materials include:
Tool Geometry
The geometry of the tool can also have a substantial impact. Here are key aspects to consider:
Getting the cutting parameters right can significantly impact the quality of the final product. Key parameters include:
Feed Rate
Spindle Speed
Depth of Cut
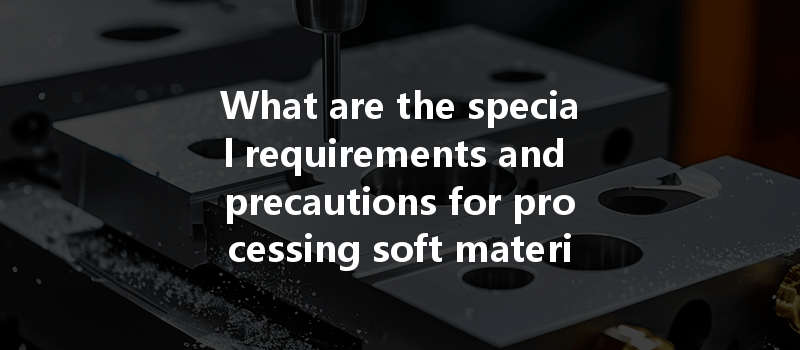
The right cooling and lubrication strategy can greatly improve the performance of processing soft materials:
Flood Coolant
MQL (Minimum Quantity Lubrication)
It is crucial that CNC machines are properly calibrated and programmed:
Regularly testing and measuring the outputs is essential for maintaining quality:
First Article Inspection
Ongoing Monitoring
Precautions to Take When Machining Soft Materials
As soft materials can deform under high temperatures, it is crucial to monitor the thermal state throughout the machining process. Implement sufficient cooling measures and avoid excessive speeds that could lead to overheating.
Burr formation is more prevalent in soft materials. Precautions include:
Improper handling and storage of soft materials can introduce defects:
Implementing a tool maintenance schedule can significantly reduce the risk of failure and inconsistent results:
: Mastering the Art of Machining Soft Materials in CNC
Processing soft materials in CNC machining involves a careful blend of art and science. From selecting the right tools to being aware of unique material characteristics, every detail matters to gain efficiency and product quality. Understanding the vast array of factors influencing machining performance can significantly elevate the manufacturing process.
Why This Blog Matters
In a fast-evolving industry, the ability to achieve precision and efficiency in machining soft materials can be a game-changer. As demand for lighter, more versatile materials continues to grow, mastering the special requirements and precautions for CNC machining in this domain will not only enhance manufacturing practices but also impact broader economic scales.
Investing time in understanding these guidelines not only promises better output but also contributes to sustainability through less material waste and improved production methodologies. Whether you’re a seasoned machinist or a newcomer, the principles laid out in this blog can prove invaluable in your quest for machining excellence. Stay informed, apply these techniques, and watch your capability soar in CNC machining of soft materials.