Did you know that CNC machining is responsible for manufacturing over 30% of all parts in the United States? This powerful technology supports industries ranging from aerospace and automotive to medical devices, owing its effectiveness to its ability to work with various materials. However, as versatile as CNC machining is, it presents unique challenges when processing different material properties. How does a machinist adjust their approach to meet the diverse needs of metals, plastics, and composites? This question encapsulates the essence of CNC machining’s complex world.
—
Understanding CNC Machining
Before diving into the specific challenges and solutions for various materials, it is essential to understand what CNC machining entails. CNC stands for “Computer Numerical Control,” a technology that utilizes computers to control machine tools. This process allows for precise and automated manufacturing, enabling the production of complicated shapes and designs that would be virtually impossible by hand.
Why Different Material Properties Matter
Every material has its unique physical and mechanical properties, which influence the machining process. Factors such as hardness, tensile strength, thermal conductivity, and ductility determine how a material behaves during machining. It’s crucial for manufacturers to understand these properties to optimize their machining processes and achieve desired results.
Common Material Categories in CNC Machining
Unique Challenges in Machining Different Materials
Challenge: The inherent hardness of metals like stainless steel or tool steel can lead to rapid wear on cutting tools and may require stronger tooling materials and altered parameters to maintain efficiency.
Solution:
Challenge: Plastics can exhibit issues such as melting, deformation, or chipping during machining due to their lower heat tolerance compared to metals.
Solution:
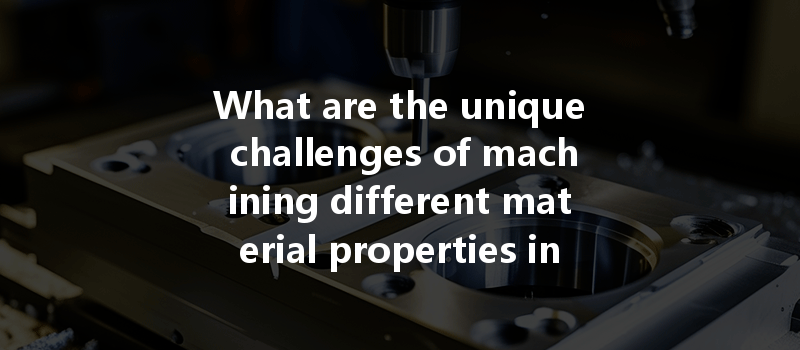
Challenge: Composites often consist of different layers and materials, leading to variability in machining behavior. The risk of delamination or uneven wear necessitates careful process control.
Solution:
Strategies for Material-Specific Machining
A. Pre-Processing Techniques
Understanding material properties in greater depth can provide insights for pre-processing adjustments:
B. Real-Time Monitoring
Incorporate in-process monitoring systems that allow for data collection on tool wear, temperature fluctuations, and material performance:
C. Post-Processing Techniques
Adopting post-processing approaches can substantially enhance the overall product quality:
Exploring Advanced Technology and Innovations
As the manufacturing industry evolves, emerging technologies continually reshape the landscape of CNC machining:
The Importance of Selecting Suitable Materials for CNC Machining
Properly matching materials with specific machining processes enhances efficiency and product quality. Selecting the right materials not only reduces production costs but also impacts lead times and sustainability of the manufacturing process. A well-optimized material-handling strategy ensures that parts are produced to the highest quality with minimal waste, achieving both performance and profitability.
: Navigating the Complex CNC Landscape
The challenges faced in CNC machining are nuanced and multifaceted. Each material presents its own set of properties that demand tailored approaches and techniques. By understanding these properties—from metals to plastics to composites—manufacturers can devise effective solutions, enhancing machining efficiency and product quality.
Investing time and resources into understanding the unique challenges of various material properties doesn’t just yield better machining outcomes—it fosters innovation, empowers manufacturers to adapt to industry demands, and ultimately drives advances in technology. The future of CNC machining lies in our ability to navigate these complexities and turn them into opportunities for growth and success. Engaging with these strategies and insights is crucial for anyone involved in the manufacturing landscape, ensuring competitiveness and relevance in a rapidly evolving market.