Did you know that stainless steel accounts for approximately 70% of the total metal fabrication market? Among various grades, 347 stainless steel stands out as a prominent choice for industrial applications due to its corrosion resistance and high-temperature strength. However, many engineers and manufacturers often grapple with its weldability during CNC (Computer Numerical Control) processing. This article dives deep into the weldability of 347 stainless steel, uncovering its significance, potential issues, and comprehensive solutions to optimize its use in CNC machining.
1.1 Properties and Composition
1.2 Applications
2.1 What is Weldability?
2.2 Why is Weldability Important?
3.1 Sensitivity to Heat
3.2 Intermetallic Compounds Formation
3.3 Cracking during Welding
4.1 Pre-Welding Preparation
4.2 Choosing Appropriate Filler Materials
4.3 Control of Heat Input
4.4 Post-Weld Heat Treatment
5.1 TIG Welding
5.2 MIG Welding
5.3 Laser Welding
6.1 Tool Selection
6.2 Cutting Parameters
6.3 Inspection and Quality Control
7.1 Aerospace Industry Application
7.2 Chemical Processing Equipment
1.1 Properties and Composition
347 stainless steel is a chromium-nickel alloy that contains niobium, making it highly suitable for high-temperature applications. It exhibits excellent corrosion resistance, particularly against sulfuric and phosphoric acids, while maintaining exceptional joint integrity after welding. The elements in 347 stainless steel lend it a distinct advantage in terms of durability and thermal stability.
1.2 Applications
You will commonly find 347 stainless steel in applications where heat and corrosion resistance are critical. Industries such as aerospace, chemical processing, and energy generation utilize this alloy for producing components like exhaust systems, furnace parts, and heat exchangers.
2.1 What is Weldability?
Weldability refers to the ability of a material to be welded without experiencing defects. It encompasses several factors, including the material’s properties, the welding technique employed, and environmental conditions.
2.2 Why is Weldability Important?
In CNC processing, weldability is paramount for creating strong and reliable joints. Poor weld quality can lead to structural failures, increased costs, and project delays. Therefore, understanding the characteristics of 347 stainless steel is essential for ensuring successful outcomes in fabrication.
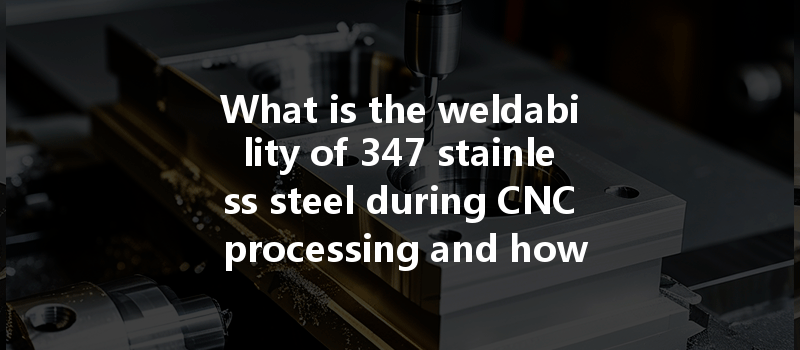
3.1 Sensitivity to Heat
347 stainless steel is particularly sensitive to heat, making it susceptible to warping and distortion if not managed carefully during welding. This sensitivity can result in inconsistent joint quality and mechanical properties.
3.2 Intermetallic Compounds Formation
The presence of additional elements in the composition may form intermetallic compounds at the weld interface. These compounds can reduce the toughness of the material, ultimately impairing its performance.
3.3 Cracking during Welding
Cracking is a significant concern when welding 347 stainless steel. Factors such as thermal stress, inadequate welding parameters, or unsuitable filler materials can lead to undesirable cracking, jeopardizing the integrity of the weld.
4.1 Pre-Welding Preparation
Proper pre-welding preparation is crucial for success. This includes cleaning the base materials to remove contaminants, aligning parts accurately, and selecting the right fixture to minimize distortion during welding.
4.2 Choosing Appropriate Filler Materials
Selecting the right filler material is imperative for maintaining weld quality. For 347 stainless steel, matching the filler composition closely can provide better mechanical properties and corrosion resistance in the final joint.
4.3 Control of Heat Input
Managing heat input involves determining the proper welding parameters such as voltage, amperage, and travel speed. Consistent heat management will help prevent overheating and ensure the structural integrity of the weld.
4.4 Post-Weld Heat Treatment
Post-weld heat treatment can enhance the properties of welded joints by relieving residual stresses and eliminating any potential intermetallic compounds formed during welding. Various techniques, such as solution annealing, can significantly improve the toughness and ductility of the finished weld.
5.1 TIG Welding
Gas Tungsten Arc Welding (TIG) is an effective method that provides excellent control over heat input and allows for high-quality welds with minimal defects.
5.2 MIG Welding
Metal Inert Gas (MIG) welding is also commonly used for 347 stainless steel but requires careful parameter adjustments to prevent issues such as porosity and improper fusion.
5.3 Laser Welding
Utilizing laser welding is advantageous for high precision and speed. It minimizes heat-affected zones, reducing the risk of deformation and ensuring a robust weld.
6.1 Tool Selection
Using the right tools for CNC processing is essential. Carbide tools with proper coatings enhance cutting performance and longevity.
6.2 Cutting Parameters
Establishing optimal cutting speeds, feed rates, and depths can significantly impact tool life and surface finish quality, ensuring precise tolerances in your machined parts.
6.3 Inspection and Quality Control
Establishing rigorous inspection protocols before and after welding is vital. Non-destructive testing methods can identify potential defects early in the process.
7.1 Aerospace Industry Application
In aerospace, components manufactured from 347 stainless steel underwent specific pre-welding treatments and post-weld inspections. By employing TIG welding techniques, manufacturers achieved critical performance standards.
7.2 Chemical Processing Equipment
Chemical processing plants utilize 347 stainless steel for fabricating tanks and pipes. Implementing systematic quality control measures ensured optimal corrosion resistance and mechanical performance.
In conclusion, understanding the weldability of 347 stainless steel is essential for optimizing CNC processing and ensuring high-quality outcomes. Techniques such as careful pre-welding preparation, appropriate filler material selection, heat control, and post-weld treatment play pivotal roles in mitigating welding challenges.
Investing time in understanding and addressing these challenges not only leads to better performance and longevity of components but also opens doors to innovative applications in various industries. Thus, this blog serves as an important resource for engineers, manufacturers, and anyone involved in CNC machining, providing insight into making informed decisions for successful fabrication.
Whether you are in the aerospace industry or involved with chemical processing equipment, recognizing the significance of weldability in 347 stainless steel is crucial. By doing so, manufacturers can enhance product reliability and efficiency, ultimately shaping the future of metal fabrication.