In today’s rapidly evolving aerospace industry, the demand for drones is skyrocketing, driven by their versatility in applications ranging from surveillance to agriculture. As the need for high-quality drone components increases, CNC (Computer Numerical Control) machining has emerged as a vital manufacturing method. CNC milling, in particular, is essential for producing precision parts with intricate dimensions that guarantee optimal aircraft performance. YL Machining leverages cutting-edge technology and skilled craftsmanship to enhance accuracy and production efficiency in CNC milling for drone parts. In this comprehensive guide, we’ll explore strategies and best practices that can significantly improve CNC milling accuracy and production efficiency tailored specifically for the drone industry.
Understanding CNC Milling
Before diving into the strategies for improvement, it’s essential to understand what CNC milling entails. CNC milling is a subtractive manufacturing process that uses computer-controlled machines to create precise parts and components. The process involves the removal of material from a workpiece using rotary cutters, providing the flexibility to produce complex shapes and designs.
CNC milling machines operate on a three-axis or multi-axis coordinate system, allowing for a high degree of accuracy and repeatability. These machines are programmed using CAM (Computer-Aided Manufacturing) software, which translates CAD (Computer-Aided Design) models into machine code that guides the milling process.
The Importance of Accuracy in CNC Milling for Drones
Accuracy is paramount in producing drone components due to several factors:
Key Factors Influencing CNC Milling Accuracy
To enhance CNC milling accuracy for drone parts, it’s essential to consider several influencing factors:
CNC milling machines require regular calibration to ensure that they yield precise dimensions consistently. Machine calibration includes:
Proper machine maintenance, including daily checks and periodic professional servicing, enhances overall accuracy.
The choice of tooling is crucial in CNC milling. Factors to consider include:
The way parts are secured during machining impacts accuracy:
Fine-tuning cutting parameters can help achieve greater accuracy:
Strategies for Improving Production Efficiency
UPS says that “It’s about turning a challenge into an opportunity.” In the realm of CNC milling, such challenges can present opportunities for enhancing production efficiency. Below are several strategies YL Machining implements to achieve this:
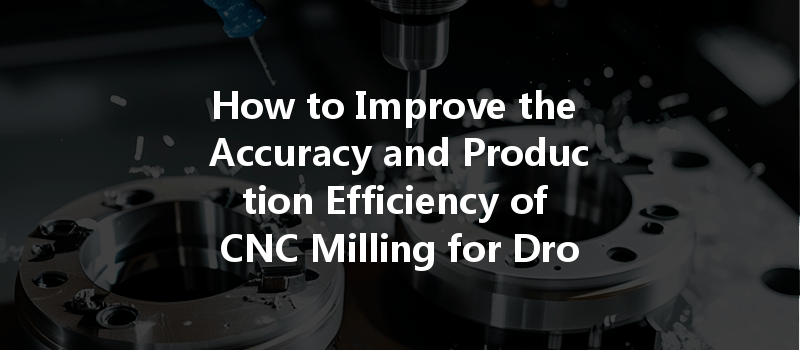
A well-structured workflow is crucial in CNC milling operations:
Incorporating automation into CNC milling processes can drastically improve efficiency:
Investing in skill development for employees is one of the most effective ways to enhance production efficiency:
Establishing a culture of continuous improvement within the organization will lead to production enhancements:
Importance of Quality Control
Quality control (QC) plays a pivotal role in CNC milling for drones. High-precision components require rigorous QC inspections throughout the manufacturing process:
Case Studies: Successful Implementations by YL Machining
At YL Machining, our commitment to excellence is reflected in several successful case studies:
Case Study 1: Drone Frame Production
Case Study 2: Propeller Manufacturing
Improving the accuracy and production efficiency of CNC milling for drone parts is a multifaceted endeavor. At YL Machining, we understand that continual advancements in technology, employee training, and process optimization are essential components for meeting the ever-growing demands of the drone industry. By implementing the strategies discussed in this guide, manufacturers can not only achieve superior precision in drone components but also enhance their overall production efficiency, leading to greater competitiveness in the market. As we look toward the future, our commitment to innovation and excellence will remain unwavering, ensuring that we meet the needs of our clients and the industries we serve.
For more information about our CNC milling capabilities and how YL Machining can assist with your next drone project, feel free to reach out to us. Let’s take your drone manufacturing to new heights!